ELBEX News
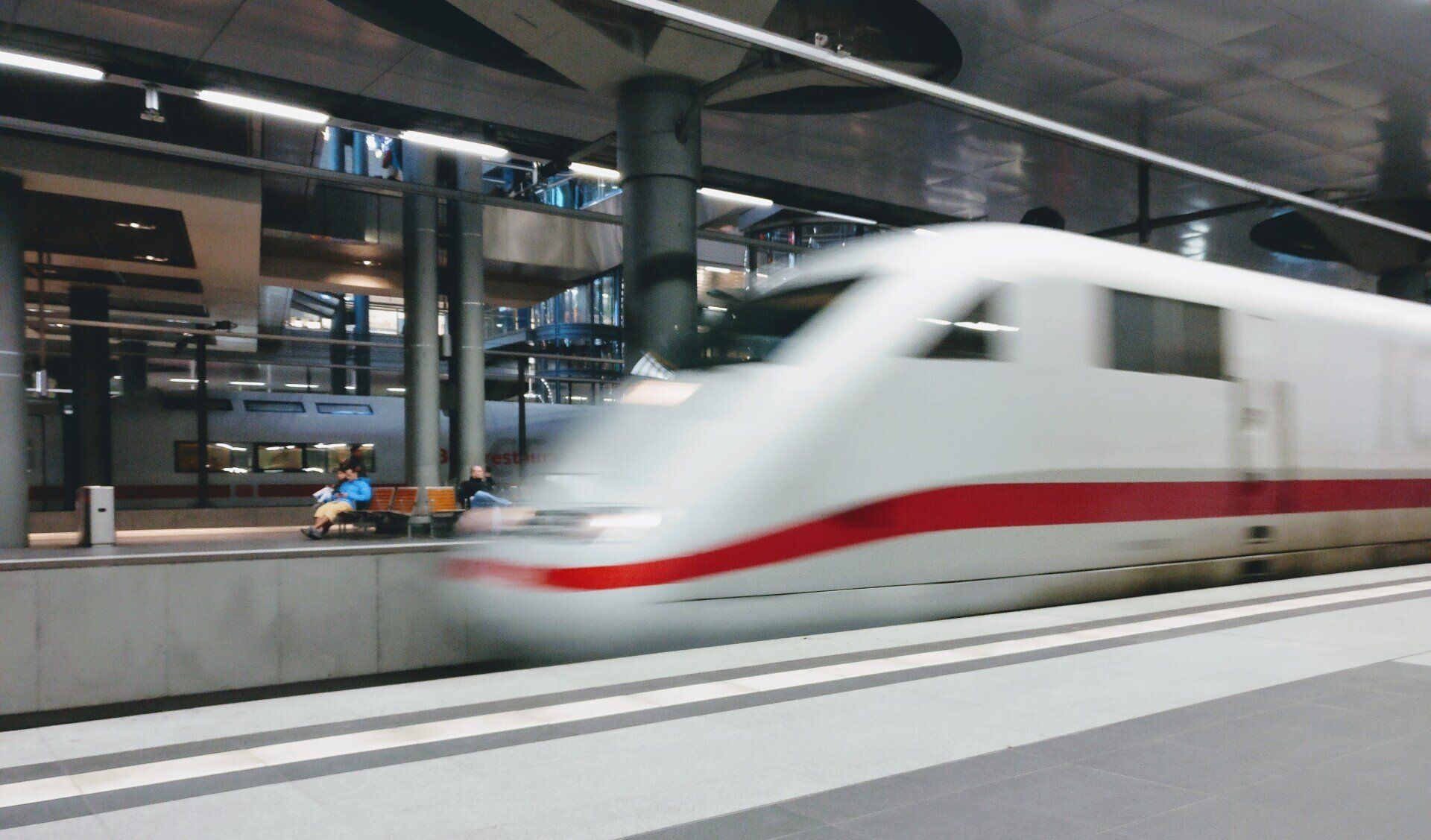
Comfortable, quiet, and reliable mass transit is essential for delivering a great experience for passengers – but overcoming the pervasive challenges of noise and vibration isn’t easy. As a leading expert in providing specialized mass transit rubber extrusions, Elbex can help you produce vibration dampening rubber components and noise reducing rubber gaskets for mass transit vehicles that are tailored to your specific needs. The Demands of the Mass Transit Environment Mass transit is subjected to constant movement and structural flexing. Powerful engines, as well as vehicle interaction with tracks or roads, generates constant noise and vibration in transit vehicles. Over time, this can impact mass transit structural integrity. Excess noise and vibration can also cause discomfort for passengers, negatively impacting how the public views your transit system. Rubber extrusions play a vital role in dampening noise and vibrations. However, achieving lasting results requires rubber components that can withstand extreme temperatures, continuous stress, varying loads, and environmental factors such as UV, ozone, and moisture exposure. Elbex's Precision in Mass Transit Rubber Extrusions Elbex is uniquely positioned to address your mass transit rubber extrusion needs. Our deep understanding of highly resilient natural rubber, weather-resistant EPDM, oil-resistant Nitrile, shock-absorbing SBR, and other rubber compounds enables us to select the right material for each application. Materials are formulated for vibration dampening, thermal stability, and durability against transit-specific stressors. Our custom profile design and engineering capabilities are another valuable strength. Our team can collaborate with your transit engineers and designers to ensure perfect fit and functionality, even for complex sealing and dampening needs. Our extrusion and molding processes are designed for tight tolerances and consistent quality, while our ISO certifications guarantee the reliability and durability of each rubber extrusion. Core Solutions for Enhanced Transit Performance At Elbex, we offer a wide range of rubber extrusion solutions that can enhance transit performance. Engine mounts, suspension bushings, body mounts, and interior panel isolators isolate shocks and reduce resonant frequencies to extend vehicle lifespans, limit structural fatigue, and improve ride quality. We also produce noise reducing rubber gaskets for mass transit vehicles, including window and door seals, floor gaskets, and HVAC system seals. With the help of these acoustic and environmental barriers, your mass transit vehicles will have quieter cabins, enhanced passenger comfort, better thermal insulation, and protection against external elements like dust and water. Additional mass transit extrusions that contribute to vehicle integrity and performance include weatherstripping, bumper guards, D-seals, and custom tubing. No matter what you need, Elbex can provide high-quality, customizable solutions. Why Elbex is the Premier Choice for Mass Transit With our unmatched expertise and experience, in-depth customization capabilities, ability to produce durable and reliable components, and collaborative approach, Elbex is the go-to source for expertly manufactured mass transit rubber extrusions. Contact us today to learn more about our capabilities or to discuss your next project.
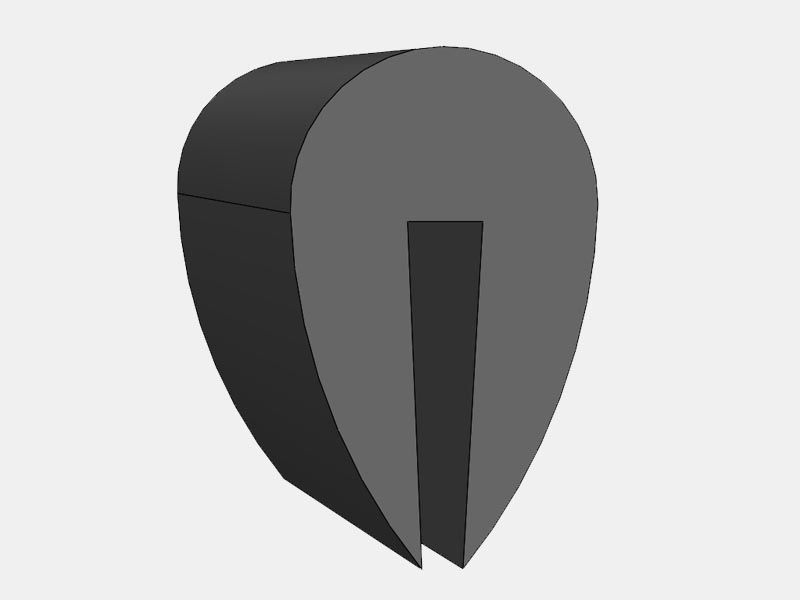
In industries like mass transit and construction, secure fitting and protected edges are key to the durability and safety of many applications. Rubber extrusions, particularly custom extruded u-channels and variations like ribbed rubber channels can play an essential role in these areas – and Elbex’s expertise in providing custom solutions will help you move forward with confidence. Understanding U-Channel Rubber Extrusions U-channel rubber extrusions are named for their distinctive U-shape, which allows them to fit over edges or within channels on mating pieces to ensure a secure fit and protect edges. The size and thickness of the legs and base should be adapted to the needs of the application, since precise dimensions are needed to get a secure fit. Depending on needs, extra features like ribbed rubber channels can be added for increased grip, vibration dampening, or sealing. As with other rubber extrusions, various materials, such as EPDM, neoprene, or silicone can be used for U-channels. The right material depends on the application’s environmental conditions (like temperature, chemicals, and UV exposure), as well as performance requirements such as flexibility and durability. Diverse Applications Across Industries U-channels serve a variety of important functions. They can be used as edge guards to protect surfaces from damage and provide a finished look, such as in automotive door edges, metal paneling, or machinery housings. The tight fit of these rubber extrusions within the channel also dampens vibrations and prevents unwanted movement between components. This is especially important for preventing excess wear and promoting structural integrity in transportation equipment and other machinery. U-channels are also used to create seals against dust, moisture, and other environmental elements. Weatherstripping in homes and glazing seals on building and automotive systems are common examples of this. With the right materials, U-channels can provide essential protection, even in extreme environments that undergo frequent temperature changes. Elbex’s Expertise in Custom U-Channel Solutions At Elbex, we provide a comprehensive level of support in addressing your U-channel needs. Our custom design and manufacturing capabilities allow us to meet your exact design requirements and performance specifications. Our knowledgeable team can also offer design assistance, technical information, and material selection guidance. Our in-house tooling and manufacturing also lends itself to quality results. Our custom on-site tooling capabilities provide a quick, cost-effective turnaround on unique U-channel profiles. We offer a wide range of materials to meet the specific performance needs of your application. The versatility and durability of U-channels makes them an excellent fit for many projects. At Elbex, our expertise and experience in providing high-quality, custom extruded u-channels and ribbed rubber channels gives you the reliable partner you need for these essential components. Contact us today to get support for your extrusion needs.
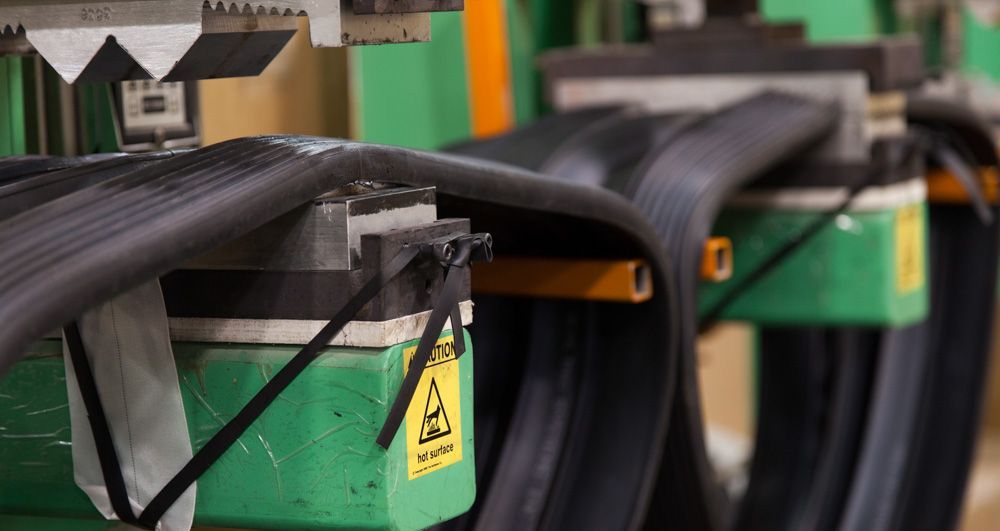
Rubber extrusions are incredibly versatile, used across a wide range of industries. At the same time, we recognize that understanding the basics of rubber extrusion for beginners can be challenging. In this blog, we’re going to provide a step by step overview of the rubber extrusions process, and how Elbex’s approach to the rubber extrusion process can benefit your company. The Fundamentals of Rubber Extrusion Rubber extrusion is a process in which uncured rubber materials (such as EPDM, silicone, neoprene, and nitrile) are forced through a shaped die. This is done to create a long, continuous profile, reducing waste and making the production of rubber extrusions more efficient. The extruder forces the rubber through the die, which can be adapted to create different shapes for different applications. The continuous profile then goes into a cooling system, where it cures and hardens. After it is cured, handling equipment allows the long profile to be cut to length to form multiple extrusions. Elbex's Streamlined Rubber Extrusion Process: A Step-by-Step Overview At Elbex, we follow a five-step process for streamlined rubber extrusion creation: Step One: Initial Consultation and Design Input. Most projects start when the client provides design information. This usually comes in the form of a drawing or sketch that provides a visual of the extrusion, or a physical sample that we can reverse engineer. Step Two: In-House Die Creation. Once we have a finished design, we manufacture our rubber extrusion dies in-house. By eliminating the need for external vendors, we can lower costs and provide a faster turnaround. This also ensures that the die is the proper shape for the extrusion. Step Three: The Extrusion Process. Once the custom-made die is ready, we use our extrusion equipment to force the heated rubber through the die. The right level of heat and pressure is essential to maintain the right shape during this step. Step Four: Curing and Vulcanization. After going through the die, the rubber is vulcanized (or cured) with chemicals like sulfur to help it harden and improve its physical traits. Step Five: Cooling and Handling. After the extrusion has cured, it needs to cool. Cooling completes the hardening process, after which the rubber can be cut to length or spooled based on application needs. Elbex’s Commitment to Your Project: Beyond the Basics At Elbex, our commitment to your project’s success goes beyond the basics. In addition to producing custom profiles catered to your specific requirements on-site, we offer technical resources to help your design team – and we can offer design assistance and troubleshooting as needed. Our experienced team can also recommend the right materials for different use cases so you can have confidence your extrusions will stand the test of time. From initial design input to the handling stage, you can count on Elbex’s efficient, client-focused approach to deliver the results you need. With in-house tooling and engineering support, we deliver dependable results that meet and exceed expectations. Whether you’re a newbie or an experienced pro, contact us today to get started on your next rubber extrusion project.
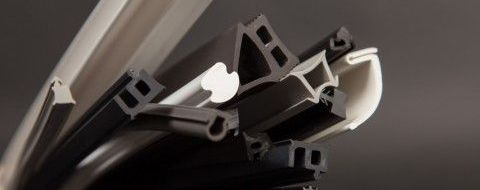
When it comes to designing custom rubber extrusions, the right team can make all the difference. As a leader in this field, Elbex provides extensive rubber extrusions engineering support. As your trusted rubber extrusions design consultancy, you can count on our team to deliver results perfectly catered to the unique needs of your applications. Dedicated Engineering Assistance: From Concept to Creation At Elbex, we understand that every project is different, requiring unique rubber extrusion design solutions to meet your specific requirements. We believe in proactively engaging with our clients early in the process to gain a full understanding of project needs and ensure better collaboration. Whether you need design support for new and innovative rubber extrusion applications or help identifying and resolving issues with existing or legacy applications, our team can help. We bring our problem-solving approach and industry knowledge to material selection, profile design, and functional considerations to provide cost-effective, high-performing solutions catered to your needs. “Hands On” Project Management: Your Dedicated Engineering Leader Our rubber extrusion design experts take a true hands on approach. By assigning a dedicated engineering team leader to each project, you get what we like to call a “quarterback” – a central point of contact and project manager who is with you every step of the way. This allows us to provide comprehensive support tailored to your needs. Whether you require visits to your location, field support during implementation, assistance with tooling design and setup, or engineering setups and consultations at our facilities, your team leader will help everything go smoothly. Leveraging Elbex’s Resources for Project Success In addition to our talented team members, we also provide a variety of engineering resources for your project. Our in-house custom tool and die design services ensure efficient, high-quality work for unique extrusion needs. We also provide a wide array of technical information to help you design your own extrusions. When needed, our team can offer design assistance and troubleshooting. We can also help you select cost-effective materials that meet required performance levels. At Elbex, our rubber extrusion design experts are committed to providing the comprehensive design and engineering support your project needs. As trusted experts and consultants, we take pride in providing results that meet and exceed expectations. Contact us today to learn more about our rubber extrusion design solutions and to start your project.
Fire safety is one of the most important considerations in any construction project. The use of fire-retardant materials helps protect occupants and keep flames from spreading. At Elbex, our ability to produce high-quality fire-retardant rubber profiles ensures that public buildings and other construction projects meet even the most stringent fire safety standards while protecting people and property. Elbex’s Expertise in Fire-Resistant Rubber Products Fire-resistant rubber products start with the right materials. At Elbex, we start by selecting and formulating rubber compounds that exhibit fire-retardant properties based on the fire safety classifications and standards you need to meet. Materials like specialized neoprene, silicone, and EPDM are all examples of elastomers that provide good fire resistance. This materials expertise is paired with state-of-the-art manufacturing and customization capabilities. Our processes ensure consistent quality, lasting durability, and tight tolerances so you can have confidence in our rubber extrusions’ reliability for fire resistance and everyday performance. We believe in using a collaborative approach with architects and designers to ensure optimal fire safety performance and seamless integration with building designs. Benefits of Elbex’s Fire-Retardant Rubber Solutions With Elbex’s fire-retardant rubber solutions, you can have greater confidence that all parts of your structure are contributing to fire safety. Preventing the spread of fire can provide crucial time for evacuating people and minimizing property damage if a fire occurs. Our fire-retardant materials meet or exceed building codes and regulations to ensure full compliance and maximum safety. With our rubber extrusions’ durability and resistance to weathering and degradation, you can also minimize maintenance needs as you future-proof a fire-safe environment. And with versatile construction applications for everything from sealing to insulation, you can ensure the entire structure is built to minimize fire danger. With our commitment to producing high-quality, custom-engineered fire-retardant rubber solutions, you can have confidence in your own ability to enhance the safety of your construction projects. Contact us today to learn more about how we can help with your specific fire safety needs.
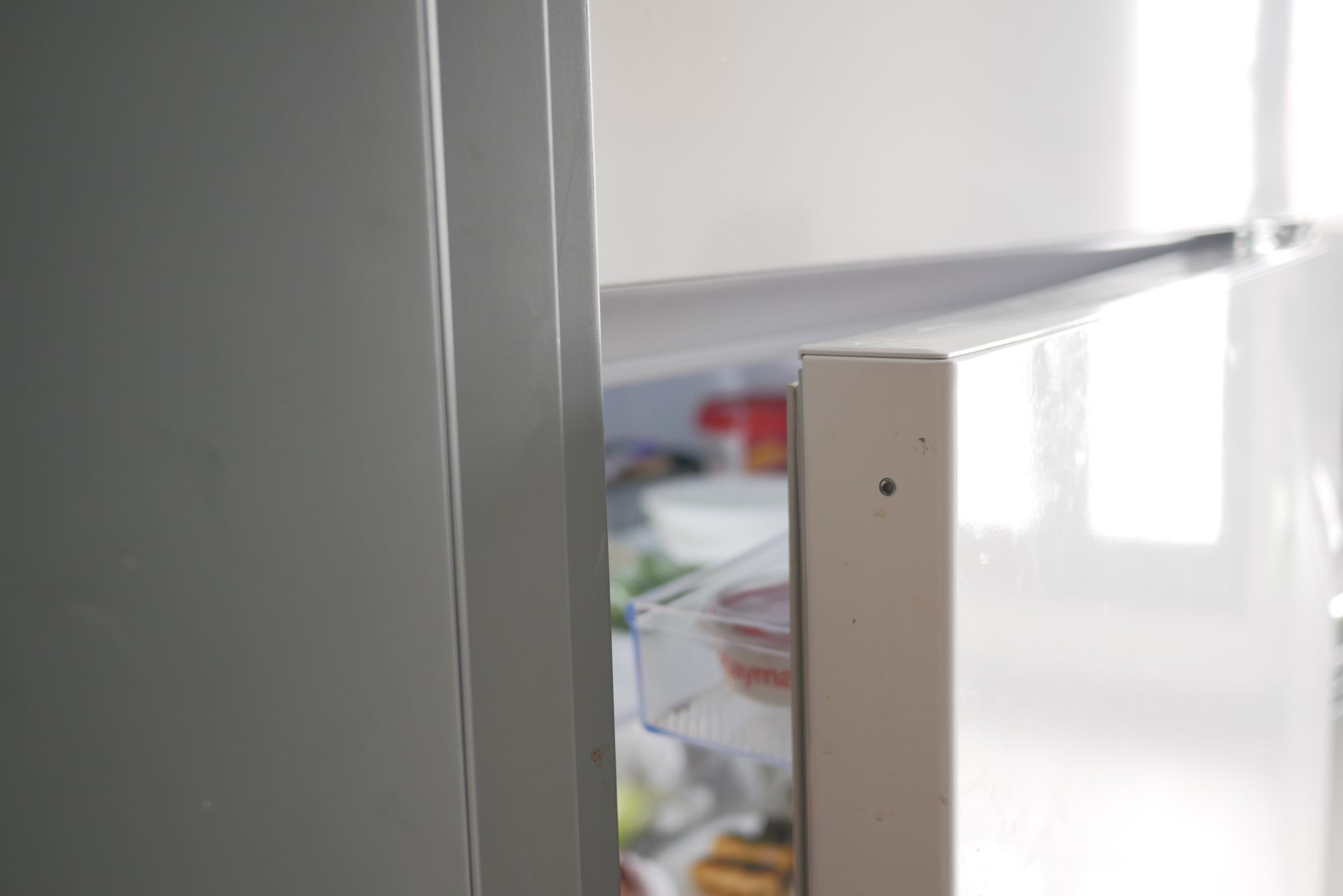
Freezer and refrigerator door gaskets play an essential role in ensuring that these appliances are energy efficient, preserve food, and prevent frost buildup. Worn or damaged gaskets can result in significant energy loss, as well as temperature fluctuations that lead to food spoilage – which can prove costly in both residential and commercial kitchens. As a leading manufacturer of high-quality, durable air barrier seals for refrigerators and freezers, Elbex ensures that your appliances deliver the quality performance your own customers deserve. The Importance of Airtight Seals in Refrigeration Properly functioning gaskets are vital in any quality refrigerator or freezer. Properly functioning gaskets prevent the escape of cold air and the entry of warm, humid air. This reduces the compressor’s workload and lowers the appliance’s energy consumption. Keeping out humid air also prevents frost buildup inside freezers, which is a common maintenance issue. Even more importantly, maintaining consistent internal temperatures extends the shelf life and quality of stored food, preventing spoilage. By reducing energy consumption and food waste, airtight seals can greatly lower costs. Elbex’s Expertise in Refrigerator and Freezer Door Gaskets At Elbex, we bring extensive experience with refrigerator and freezer door gaskets to create airtight seals specifically designed for your appliances. We use our knowledge of various elastomers to select materials like flexible PVC, TPE, and silicone that remain flexible at low temperatures, resist tearing and wear, and are food-grade compliant. We also use state-of-the-art extrusion and molding processes that ensure tight tolerances, consistent quality, and superior sealing performance. Our airtight barriers are designed for durability and longevity, even for demanding or unique applications. We can also collaborate with your manufacturing team to develop custom gasket profiles that match the specific requirements of your refrigerator and freezer models and their door configurations. Benefits of Choosing Elbex’s Refrigerator and Freezer Door Gaskets When you work with Elbex, you can have confidence that our precision-designed seals will deliver consistent, long-lasting performance. From materials selection to design, our gaskets will resist cracking, tearing, and compression set, even on frequently used refrigerators and freezers. We also ensure that our gaskets are easy to install and replace, minimizing downtime when maintenance is needed. And with our customization options, we can tailor everything from aesthetics to functionality based on your specific needs. At Elbex, we are committed to providing high-quality, custom-designed refrigerator door gaskets and air barrier seals for refrigerators and freezers. As an appliance manufacturer or service provider, you can count on Elbex to help you achieve optimal refrigeration performance. Contact us today to learn more.
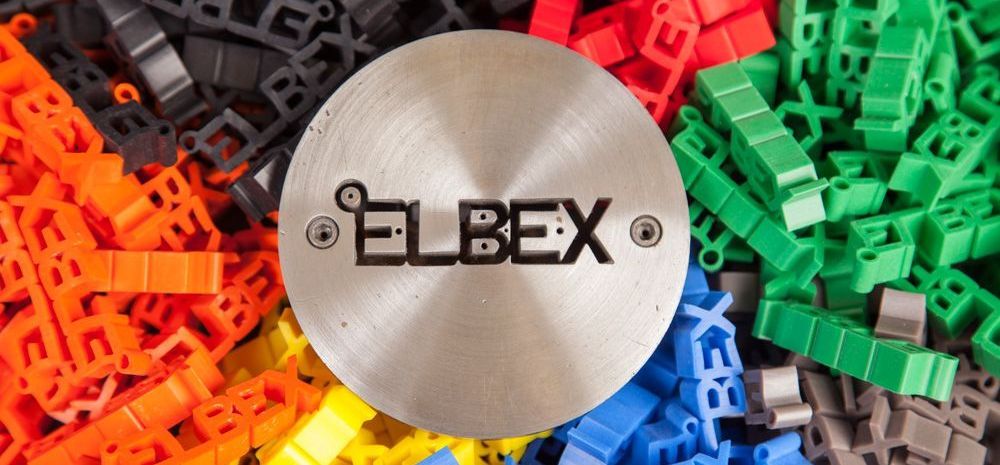
At Elbex, we are committed to producing high-quality rubber extrusions, no matter what industry you work in. Why can you trust us? A big part of the reason is because of our ISO (International Organization for Standardization) certification in the manufacturing industry. Here’s a closer look at what this means for our work. Understanding the Value of ISO Certification The ISO sets international standards for various industries. It is an independent group that is recognized and respected worldwide for its focus on ensuring that products and systems are safe, high-quality, and consistent. Companies must meet specific requirements to achieve and maintain certification. An important aspect of ISO certification is that it’s not a “once and done” certification. It requires ongoing adherence, with regular audits to stay certified. Essentially, ISO certification means Elbex operates according to internationally recognized best practices. Elbex’s Commitment to Quality Through ISO Standards ISO certification is a reflection of our own standards of customer satisfaction, consistent quality, and continuous improvement. Our ISO-certified Quality Management System (QMS) focuses on understanding and meeting customer needs, including by collecting and applying feedback from our clients. Our manufacturing processes are documented and controlled to ensure they are consistently applied with every project to ensure product uniformity and quality. At the same time, we proactively look for ways to improve our processes, products, and services, including through corrective and preventive actions when needed. Why Clients Can Trust Elbex’s Expertise ISO certification means you can have confidence that our rubber extrusions are manufactured to the highest quality standards, with minimal risk of defects or inconsistencies. Our standardized processes also mean you can enjoy clear communication and well-defined procedures at every step of the process. With an ISO-certified supplier like Elbex, you can have peace of mind from knowing that we adhere to international best practices, while also being committed to growing long-term, trustworthy partnerships. Our goal is to be a reliable partner you can turn to anytime you need rubber extrusion services. At Elbex, we’re proud to have obtained ISO certification as a testament to our dedication to quality, customer satisfaction, and continual improvement. Experience the Elbex difference for yourself – contact us today to request a quote or learn more about our ISO-certified work.
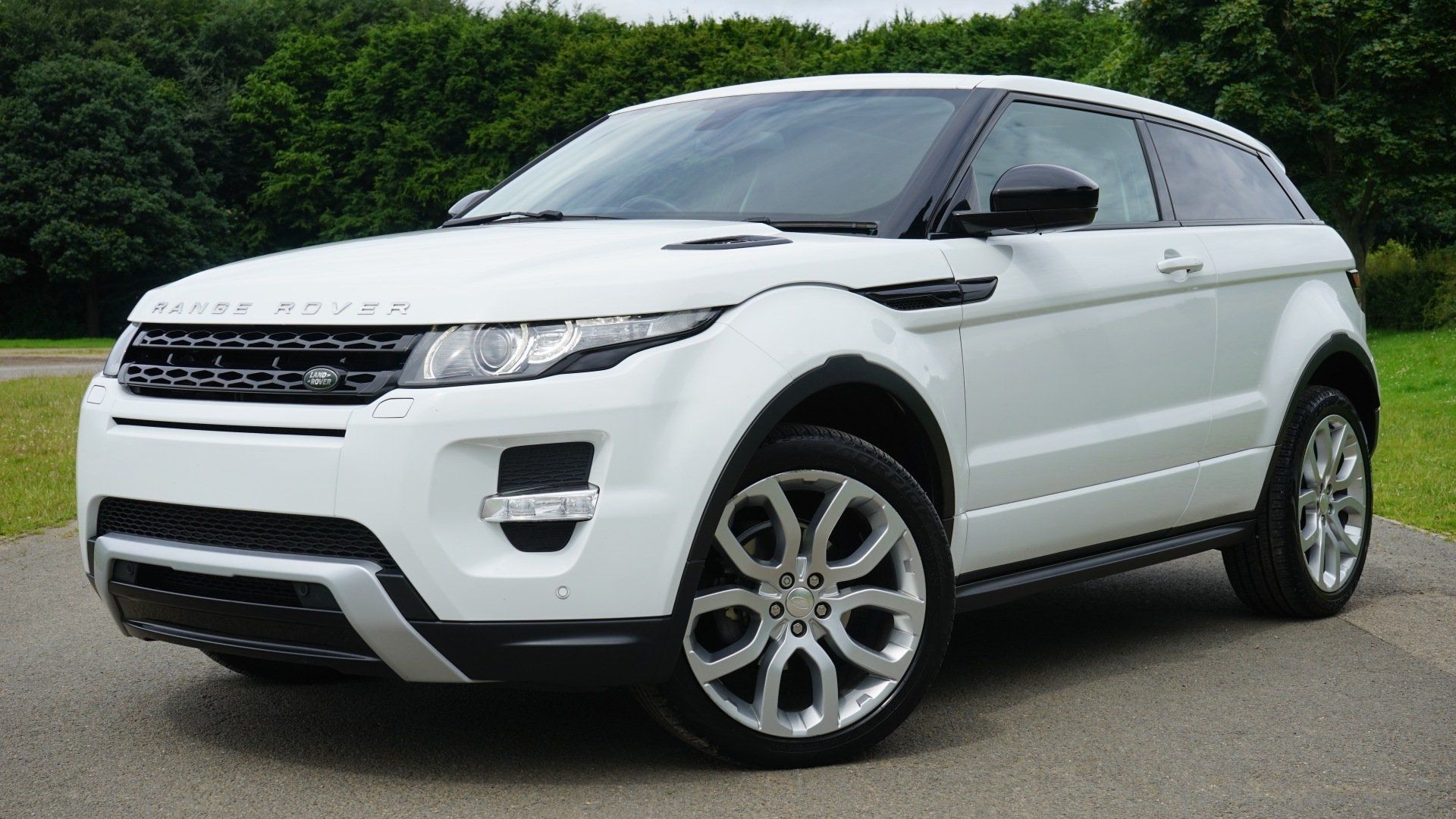
D-section rubber profiles are some of the most commonly used rubber seals, particularly in the automotive, construction, and appliances industries. The distinctive shape of extruded D seals protects components, prevents leaks, and ensures optimal performance. Here’s how Elbex creates high-quality D-section rubber seals for your needs. What are D-Section Rubber Seals? A D-section rubber seal is a half-round rubber seal with a distinctive D-shaped cross-section. D-seals are available in a wide range of height and width variations to meet the needs of different applications. Many also utilize adhesive backing for easier installation, or metal inserts for added structural support. When to Use D-Section Seals D-seals are especially common in the automotive and construction industries, where they are used to seal doors, windows, and hatches. They create watertight seals that can also reduce noise and vibrations and improve insulation, protecting equipment and components from dust, moisture, and debris. Because of these and other environmental hazards, D-seal design and material selection must account for temperature, pressure, chemicals, the material’s compatibility with the sealing surface, and the required force to create the seal. Advantages of D-Section Rubber Seals D-section rubber seals offer superior sealing performance. When the D-seal is compressed, it creates a tight seal that keeps out leaks and contaminants. Since D-seals can be adapted to different shapes and sizes, they are extremely versatile. They are also typically very easy to install, often using simple press-fit or adhesive applications. When high-quality materials are used, you can count on D-seals to offer extended durability, while still being more cost-effective than other sealing solutions. The combination of performance and value makes them the go-to choice for many sealing applications. Why Choose Elbex’s D-Section Seals? Elbex can help you get the best possible outcomes from using D-seals thanks to our materials expertise and custom design capabilities. Our knowledge of elastomer properties allows us to select the best material for your D-seal application. Our customization capabilities allow us to adapt the shape and size of your D-seal to fit your specific use case, even when tight tolerances are required. We can also help with additional services like vulcanized splicing, cutting, printing, and taping. Finally, with our state-of-the-art manufacturing processes and rigorous quality control measures, we ensure tight tolerances, consistent quality, and superior performance that meets or exceeds industry standards. With versatile, high-quality rubber D-section seals and extensive customization capabilities, Elbex offers the versatility and quality you need for your applications. To learn more about our D-section seals, contact us today.
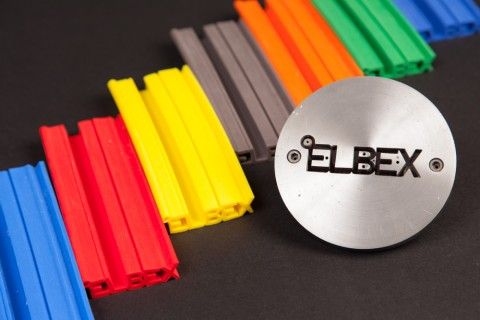
Rubber elastomers are used in countless industries and applications, from automobiles to architecture. However, understanding the physical properties of rubber elastomers is essential for getting the right material for the right application. At Elbex, our deep understanding of elastomer characteristics ensures you’ll get the right match for your project. Key Properties of Rubber Elastomers The following properties are critical when considering which rubber elastomer is right for your application: Elasticity and resilience: Rubber has the ability to deform under stress and then return to its original shape. Important in vibration damping and shock absorption. Tensile strength and elongation: The ability to stretch and withstand pulling forces without breaking. Hardness: Is the rubber flexible or rigid? This affects its abrasion resistance and compression set. Compression set: Compression set is a permanent deformation that occurs after prolonged compression. Long-term sealing or cushioning applications require a low compression set. Temperature resistance: The elastomer’s ability to withstand high and/or low temperatures – important when considering the application’s operating temperature range. Chemical resistance: An elastomer’s resistance to any chemicals, oils, and solvents that might be present in its operating environment. Weathering and ozone resistance: The elastomer’s ability to withstand sunlight, ozone, and other environmental factors are especially important for outdoor applications. Common Types of Elastomers and Their Applications The following are some of the most common types of rubber elastomers: Natural Rubber (NR): Used for tires, footwear, and adhesives, natural rubber is known for offering excellent elasticity, resilience, and tear resistance. Styrene-Butadiene Rubber (SBR): This cost-effective elastomer offers good abrasion resistance. It is commonly used in tires, conveyor belts, and footwear. Ethylene Propylene Diene Monomer (EPDM): EPDM offers excellent resistance to weathering, ozone, and heat. As a result, it is the go-to option for rubber roofing, as well as automotive seals and hoses. Nitrile Rubber (NBR): With resistance to oil, fuel, and chemicals, nitrile is commonly used for automotive and industrial seals and gaskets. Silicone Rubber (VMQ): Usable in a wide range of temperatures, while also offering excellent electrical insulation properties and biocompatibility, silicone is a top choice for medical devices, cookware, and electronics. Neoprene Rubber (CR): Neoprene’s flame resistance, oil resistance, and weather resistance means it is frequently used for applications such as wetsuits, adhesives, and automotive components. Elbex: Your Partner in Elastomer Solutions At Elbex, we combine an extensive elastomer portfolio (including custom formulations) with industry-leading technical expertise. You can have confidence in our ability to help you choose the right elastomer based on your specific project needs and desired rubber elastomer properties. Contact us today so we can help you make informed materials choices.
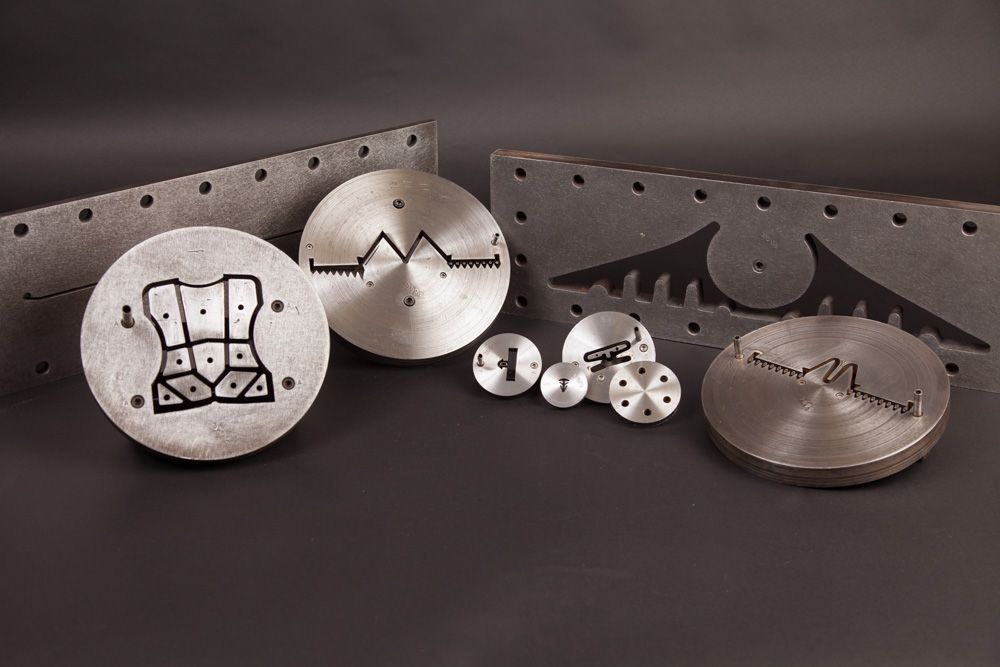
Rubber extrusions play a vital role in modern architecture. Architectural rubber extrusions are used for weatherproofing, sealing and even aesthetics. As an experienced manufacturer of custom extruded rubber for architectural applications, Elbex can provide solutions that meet the specific demands of your architectural projects. Elbex’s Expertise in Architectural Rubber Solutions The Elbex team brings decades of experience to produce successful architectural rubber extrusions. We start by using our knowledge of how different rubber compounds like EPDM and silicone match up to different architectural needs, like weather resistance and UV stability. We strive to choose materials that meet performance requirements while still matching the building’s design. This material knowledge is complemented by our advanced design capabilities. Our state-of-the-art manufacturing facilities and processes allow us to ensure tight tolerances and quality control throughout manufacturing. Our use of cutting edge software and engineering expertise, combined with our collaborative focus when working with architects and designers, also enables us to produce high-quality custom extrusions. Benefits of Elbex’s Custom Rubber Extrusions For Architecture Custom rubber profiles for architecture offer several distinct advantages. Custom profiles that are adapted to specific architectural needs lead to improved energy efficiency, weatherproofing, acoustics, and fire safety in buildings. The design freedom offered by our custom engineering also allows architects and designers to maintain the building’s aesthetic appeal without sacrificing functionality. Finally, by ensuring the right material mix is used, you can have confidence that our rubber extrusions will resist weathering and degradation. Long-term performance will greatly reduce your building maintenance costs. Applications of Elbex’s Architectural Rubber Extrusions There are many applications for architectural rubber extrusions, but the following are some of the most popular: Window and door seals: Airtight and watertight seals for doors and windows dramatically improve a building’s energy efficiency. We can create custom profiles that match unique window designs. Curtain wall systems: Rubber extrusions can help seal and weatherproof curtain wall systems, improving the building’s aesthetics and structural integrity. Expansion joints: Expansion joints accommodate movement in structures from temperature changes, settling, or soil expansion. This prevents cracks and other potential damage. For high-quality custom rubber profiles for architecture, you can count on Elbex. With our custom engineering and design capabilities, we are uniquely equipped to help architects, designers, and construction professionals bring their vision to life. Contact us today to get started.