Harnessing the Power of Rubber: Trends and Innovations in Rubber Extrusion
The use of rubber extrusions has been on the rise in many industries in recent years. With flexible manufacturing and dependable performance, rubber extrusions serve a variety of useful roles, from dampening vibrations to creating airtight seals.
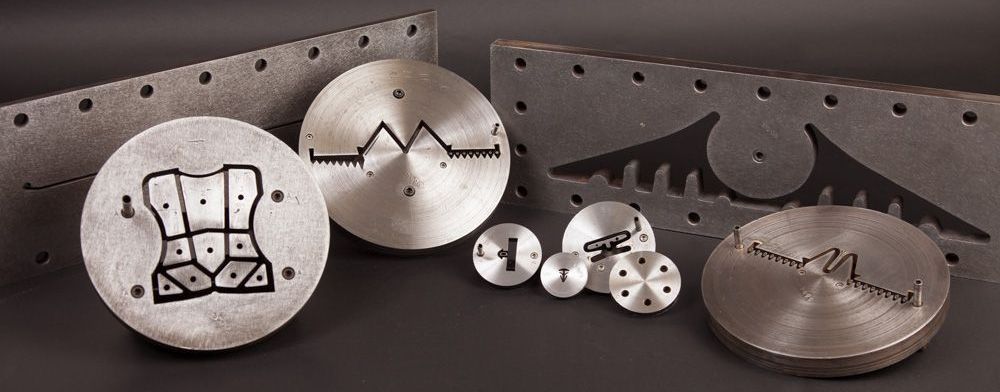
The Evolution of Rubber Extrusions
The idea of extruding materials to achieve a specific shape goes back to the late 1790s, when extruders were used to make lead pipes. As rubber began to be used, extrusion machines were adapted to force synthetic or natural rubber through a shaped die to achieve a desired shape. The pliable rubber would then be vulcanized or hardened. The introduction of new die options and the development of new elastomers has allowed for extrusions to be used in an ever-widening range of applications.
How ELBEX Pioneers Innovations in Current Market Trends
In modern times, the rubber extrusion industry has seen a shift toward more demand for custom extrusions and in-house tooling — key areas where ELBEX has proven itself as an established leader. Experience in 2-D modeling and AutoCAD design enables custom tool and die design services for any application. And with custom on-site tooling, production becomes more efficient, with shorter lead times and improved delivery. This commitment to quality has enabled ELBEX to achieve ISO certification.
Custom capabilities allow ELBEX to produce extrusions for a wide range of industries. For example, we produce automotive applications such as hinge covers, no-rattle pads for spare tires, door and window seals, gaskets, and acoustic covers. In construction, common applications include weatherstripping, glazing, expansion joints, and edge trim.
As custom rubber extrusions become more advanced, their potential applications will continue to increase exponentially. With in-house tooling and custom capabilities, ELBEX is poised to lead in this important market.
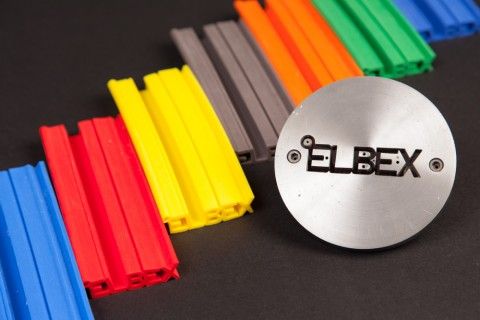
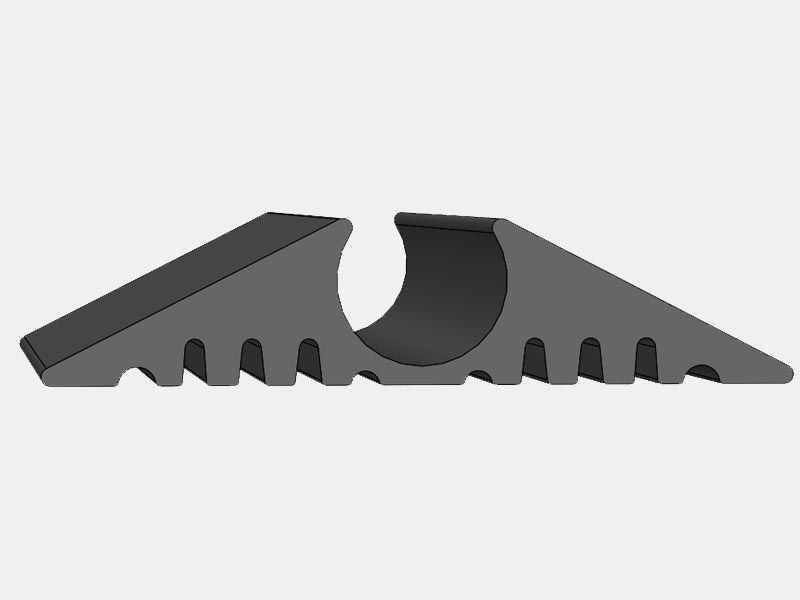
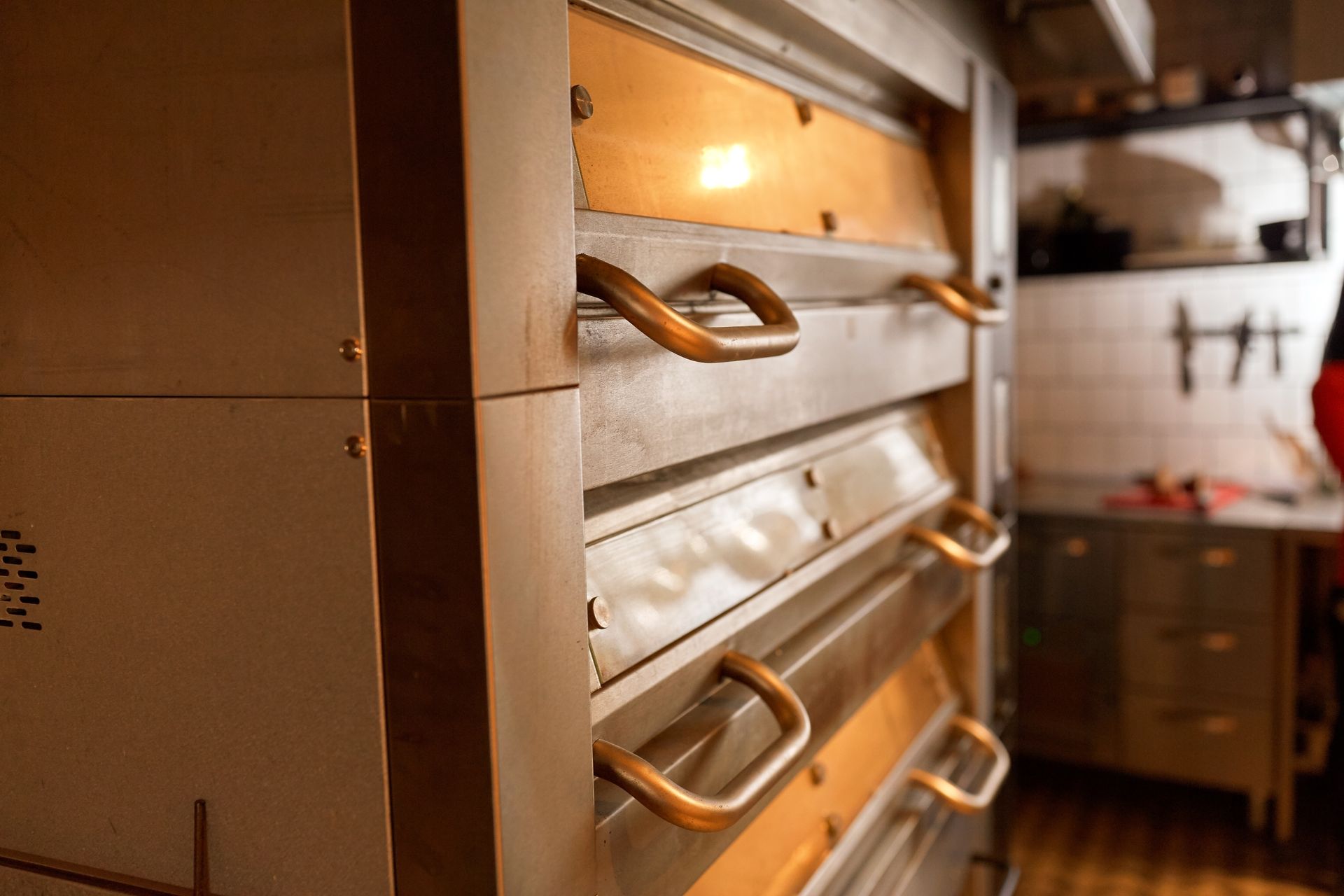