3 Mistakes to Avoid When Designing Rubber Extrusions
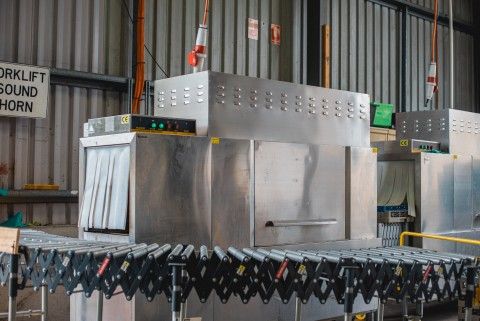
Whether you are improving an existing product or creating a brand-new product, appropriately designed rubber extrusions are vital in order to maintain consistent product quality. Here are three mistakes to avoid when designing rubber extrusions for your project
Sharp Corners
While 90-degree corners are ideal in many applications, rubber extrusions are not one of these applications. Indeed, rubber extrusions are used in many 90-degree applications, however, sharp corners in the extrusion itself can lead to leaks. It is best to include a small radius in the sealing surface design instead of a 90-degree angle.
Failing to Account for Movement
Since compression loads can vary greatly, compression and decompression must be accounted for when designing your part. If not taken into consideration, the part can end up too big or too small, and this will lead to leaks.
Designing it Alone
You will want to choose a supplier that has a dedicated team of highly-trained experts in their field, that can help take your vision and turn it into a reality. You will want a supplier that knows the ins and outs of the various materials available and that can help you to choose the material that will work best in your specific application
ELBEX Edge
The ELBEX Corporation has more than 25 years in the business of designing and manufacturing custom rubber extrusions for clients around the globe. Our extrusions have served companies in numerous fields, including the automotive sector, appliance makers, water control projects, mass transit, and several others. Our team is dedicated to quality throughout the entire extrusion manufacturing process. We consistently follow the following quality assurance practices:
- Incoming inspection of raw materials - allows for complete traceability
- SPC inspection during production
- 24 hour check
- Certificate of Compliance
For more information on how ELBEX can work for you, contact us today.
In order to meet the challenging requirements of a custom project, we offer in-house tool and design services and fabrication. Our profile engineering is designed for the manufacturing process in order to meet critical tolerances. The ultimate goal is to meet our customers’ application fitness parameters.
We have strong SPC and quality extrusion assurance systems in place, and we are ISO certified. All of these systems are in place to ensure the best possible performance and customer satisfaction for all of our extruded products.
Our capabilities and experience matters. In our 30 years, we have created quality, custom extrusions for products around the globe. Plus, with our strong relationship with Seal Master we have high quality resources at our fingertips.
There isn’t much we haven’t seen, so call us today to help bring your project to life.
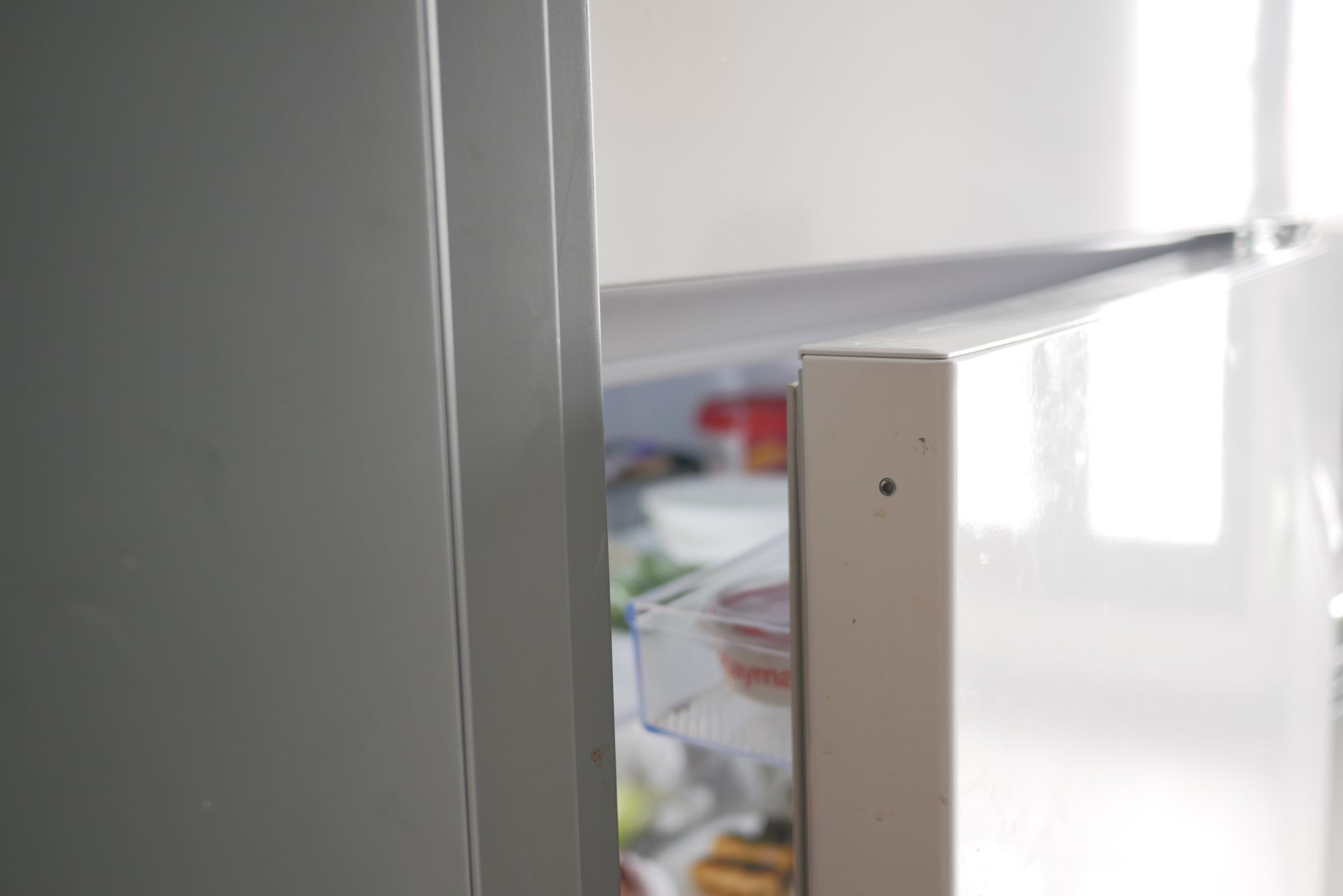
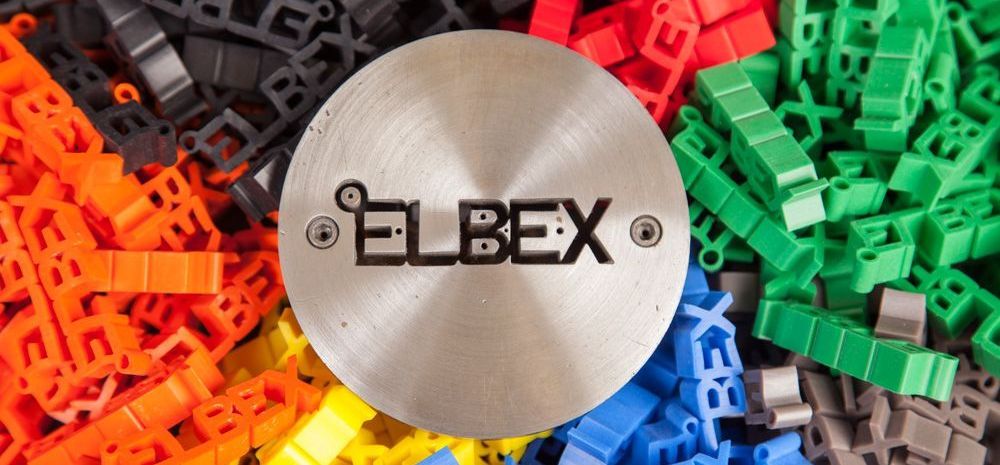