The Benefits of EPDM
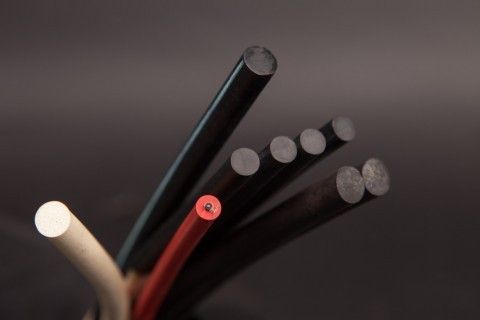
EPDM, short for ethylene propylene diene monomer, is a highly versatile synthetic rubber that is suitable for use in a variety of applications. There are two basic types of EP rubber available in today's market—EP and EPDM. EP is a copolymer of ethylene and propylene, while EPDM is a terpolymer combining ethylene, propylene and a diene monomer. EP uses a peroxide cure system. EPDM uses a sulfur cure system.
Advantages & Applications
EPDM is an electrical insulator, has excellent deflation recovery and exhibits exceptionally good resistance to weather aging, ozone, UV exposure, water, and heat. EPDM has good to very good resistance to steam, oxygenated solvents such as acetone, animal and vegetable oils, alkalis, and brake fluids. EPDM’s dynamic and mechanical properties are, in general, between natural rubber and SBR. EPDM has a wide high and low temperature resistance, with a typical service temperature range between –65° F and +300° F.
EPDM is often used as a sealer, gasket, or membrane, able to prevent the flow of fluid while still maintaining flexibility. It provides excellent cushioning. It is often used to make seals on refrigerator and freezer doors. It is used often in the automotive industry for a variety of components such as seals, hoses, bumpers and rub strips. It can also be found regularly in industrial, construction and HVAC industries.
Limitations
EPDM is not recommended for use with mineral oil, petroleum oils, fluids, or solvents. It is not flame resistant.
For more detailed information on material selection, please see our engineering technical information page. Several PDF data sheets are available for download.
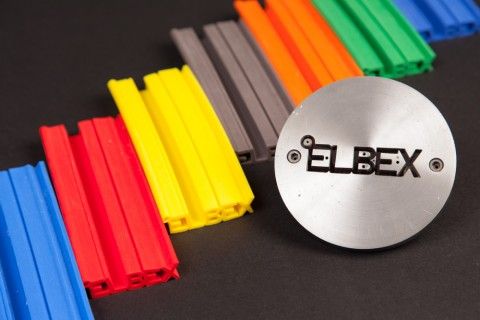
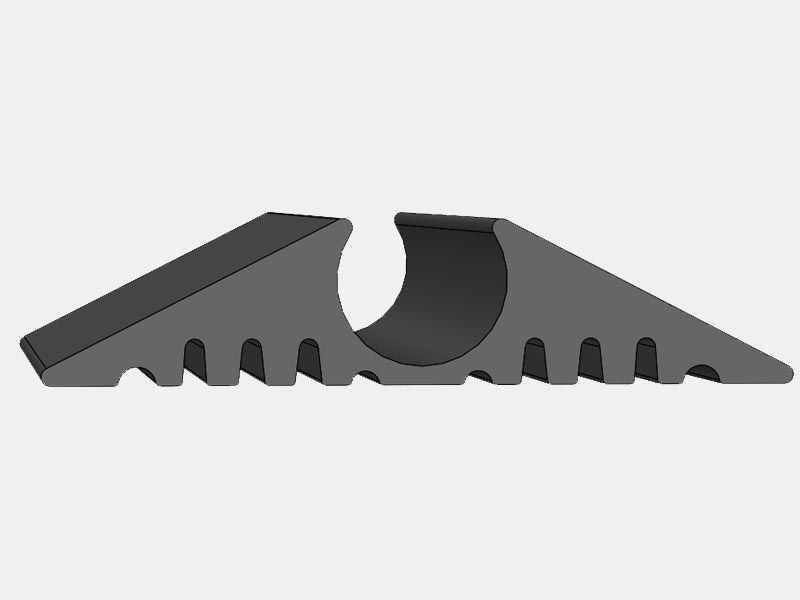
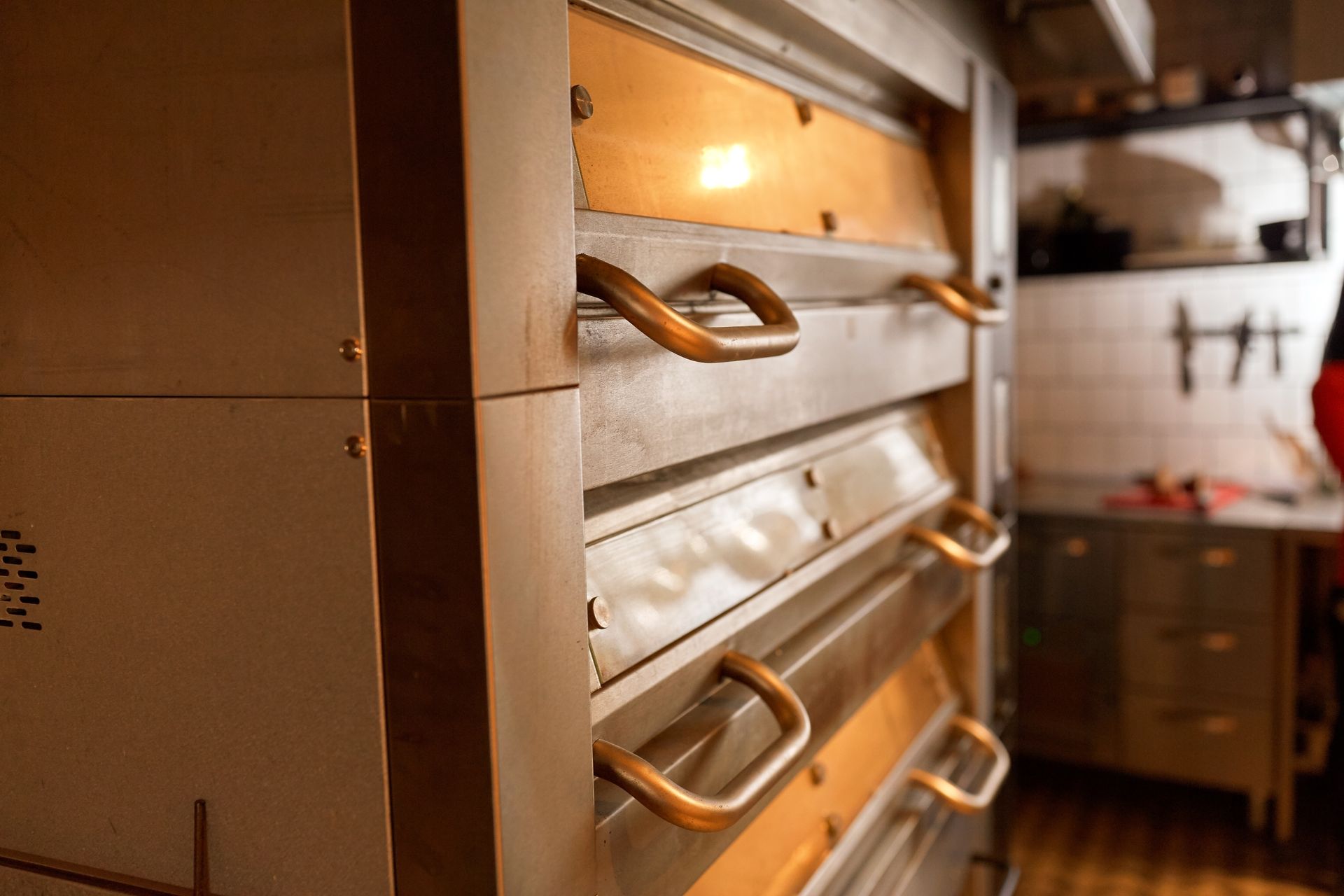