Learn More Details About Rubber Elastomer Properties

There are several common elastomeric compounds that we use at ELBEX in order to make our rub-ber extrusions and other products.
But not all elastomers are created equally and each material has different properties that make them ideal for certain uses, and not others.
Rubber compounding is a broad field. Yet basic elastomers are mixed with multiple chemicals and compounds in order to create the desired physical properties and traits. Some basic elastomers used include butyl, EPDM, natural rubber, neoprene, silicone, and others.
Each elastomer’s properties vary greatly. For instance, butyl has a poor resistance to petroleum-based fluids. It is resistant to countless other items, such as animal and vegetable fats, greases, am-monia, oxygenated solvents, and has very good weathering resistance.
Nitrile, likewise, is excellent at resisting petroleum-based fluids and has good, strong physical prop-erties. Nitrile is resistant to tearing, heat aging, abrasion, fats, oils, greases, and more.
These different elastomers are ultimately selected based on their desired use and during the die process.
Due to the unique characteristics of each material, dies are material and durometer specific. Once an uncured compound is selected, it is forced through a die and into its desired shape. After the com-pound is extruded, it is immediately cured. The ELBEX curing process involved a continuous salt bath cure line.
The extrusion process overall allows for high volume lineal foot production runs. Due to our custom abilities, minimum orders are required and are based on the material used for the extrusion.
For more information on the various elastomers and how they may be used, contact an ELBEX repre-sentative or complete an online RFQ today!
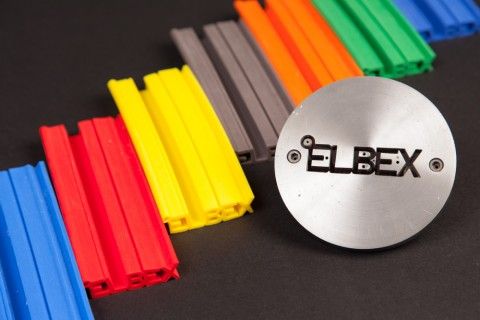
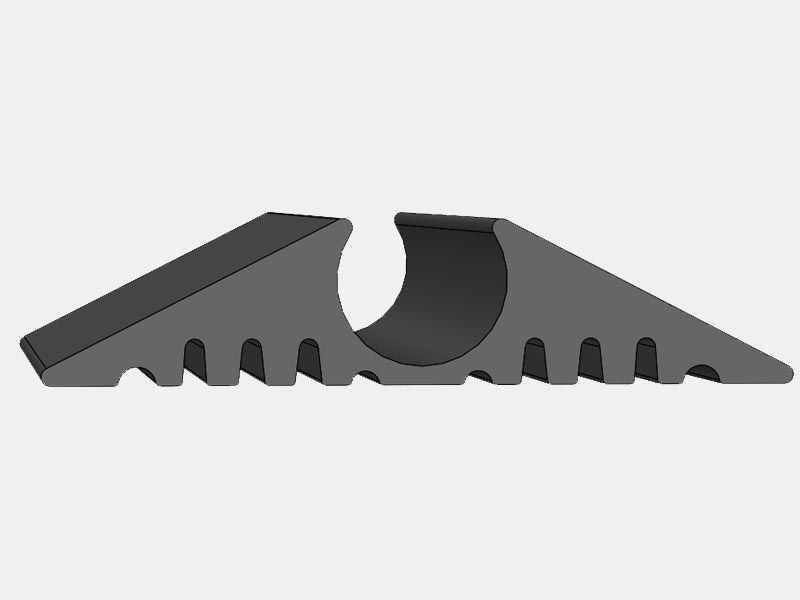
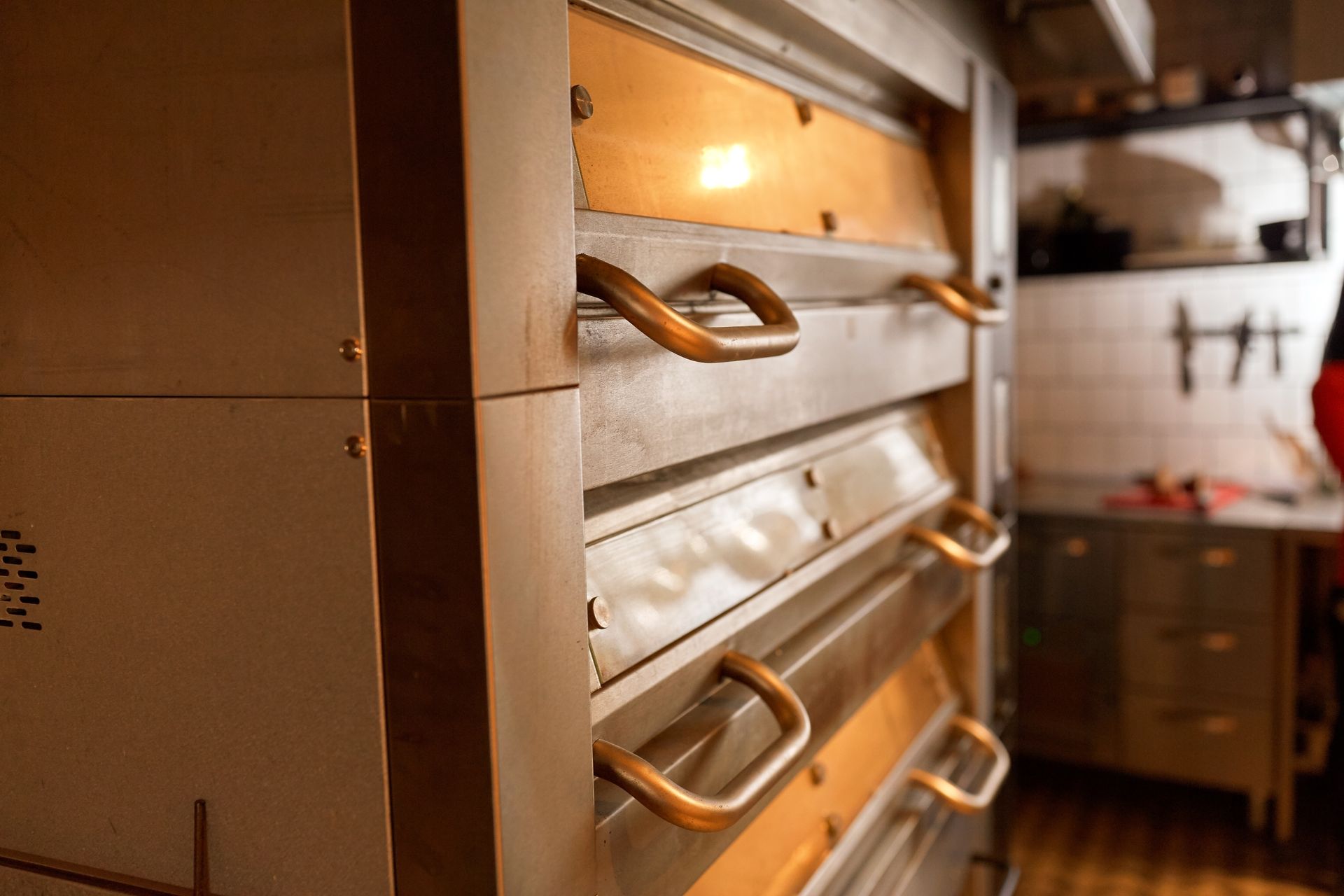